The journey of creating high-quality Expanded Polystyrene (EPS) products, from protective packaging to high-efficiency building insulation, begins with a single, critical step: the pre-expansion process. At the heart of this stage lies the EPS Pre-expander Machine. Choosing the right one is not just a technical decision; it’s a strategic investment that defines your production capacity, product quality, and operational efficiency. This guide is designed for business owners and procurement leaders like you. We will demystify the technology, compare the two main types—Batch and Continuous—and provide the insights you need to select the perfect pre expander machine that aligns with your specific manufacturing goals, ensuring you make a decision that pays dividends for years to come.
What Exactly is an EPS Pre-Expander Machine and Why is it Crucial for Your Business?
In any EPS production line, the pre-expander machine serves as the foundational starting point. Its role is singular but profoundly important: it transforms tiny, solid raw EPS beads into the lightweight, expanded beads that are the building blocks of all final EPS products. Think of it as the step that puts the "air" in "Styrofoam." The machine takes raw polystyrene beads, which contain a blowing agent (typically pentane), and uses precisely controlled steam to heat them. This process causes the pentane to vaporize and expand, puffing up each individual bead to many times its original size.
The quality and consistency achieved during this initial pre-expansion stage are paramount. Why? Because any inconsistencies in density or size introduced here cannot be corrected later in the block molding or shape molding stages. If the beads are improperly expanded, the final product could suffer from a range of defects, including poor fusion, structural weakness, or inconsistent insulation properties. Therefore, the reliability and precision of your eps pre-expander machine directly dictate the quality of your finished goods, your material usage efficiency, and ultimately, your company’s reputation in the market. Investing in a high-quality expander is investing in product excellence.
The Core of the Matter: Understanding the Pre-Expansion Process
To truly appreciate the different types of machines, it helps to understand the science behind the pre-expansion process. The magic happens inside a sealed chamber, or pressure vessel, within the expander machine. The process unfolds in a few key steps:
- Feeding: Raw EPS beads are fed into the expansion chamber from a hopper.
- Steaming: Pressurized steam is injected into the chamber. The heat from the steam does two things simultaneously: it softens the polystyrene polymer structure of the bead and heats the pentane trapped inside past its boiling point.
- Expansion: As the pentane turns into a gas, it exerts pressure from within, inflating the softened bead. This is a moment of rapid depressurization and expansion where the volume of the beads increases dramatically, while their density decreases.
- Control: The amount of steam and the duration of the exposure are the key variables. By carefully managing these, an operator can expand the beads to a precise target density (e.g., 15 kg/m³, 20 kg/m³, etc.).
- Stabilization: After expansion, the beads are discharged and often passed through a fluid bed dryer. This step removes residual moisture and begins to cool the beads, allowing them to harden in their new, expanded form before being sent to a storage silo.
Understanding this delicate balance of temperature, pressure, and time is crucial. The best machines offer advanced control systems that manage these variables with exceptional accuracy, ensuring every bead is expanded uniformly.
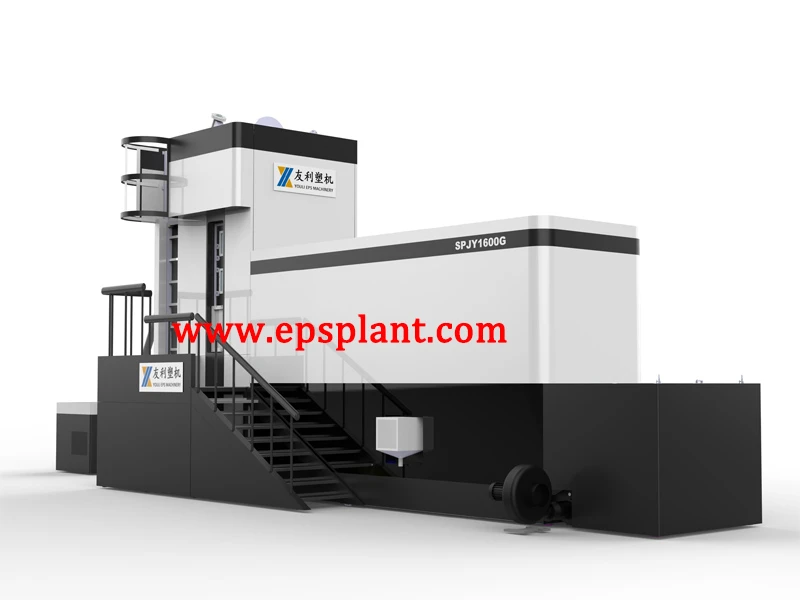
What are the Key Differences Between a Batch Pre-Expander and a Continuous Pre-Expander?
When you’re ready to purchase an eps pre-expander, your first major decision will be choosing between a batch model and a continuous model. The choice depends entirely on your operational needs, production volume, and product diversity. Both are excellent machines, but they are designed for very different production philosophies.
A batch pre-expander processes material in distinct, measured cycles. It’s like baking cookies one tray at a time. A continuous pre-expander, on the other hand, works like an assembly line, processing a constant, uninterrupted flow of material. As a seasoned machine manufacturer, I often advise clients to carefully consider their product mix. If you frequently switch between producing low-density packaging and high-density construction-grade blocks, the flexibility of a batch machine is invaluable. If your business focuses on mass-producing a single product, the efficiency of a continuous machine is unmatched.
Here is a simple table to illustrate the core differences:
Feature | Batch Pre-Expander | Continuous Pre-Expander |
---|---|---|
Operation | Processes material in discrete, separate batches. | Processes material in an uninterrupted, constant flow. |
Best For | High-precision, multiple density requirements, frequent product changeovers. | High-volume, single-density mass production. |
Density Control | Extremely precise control for each batch. Easy to change density. | Consistent density for long runs. Changing density is more involved. |
Production Capacity | Lower to medium. Limited by cycle time per batch. | Very high. Designed for maximum throughput. |
Flexibility | High. Ideal for manufacturers with diverse product portfolios. | Low. Optimized for efficiency in a single task. |
Typical Products | Custom packaging, ICF blocks, decorative items, specialty products. | Building insulation boards, large void fillers, geofoam blocks. |
How Does a Batch Pre-Expander Machine Work?
The batch pre-expander machine is the champion of precision and flexibility. Its operation is a carefully orchestrated cycle that ensures every single bead receives the perfect amount of energy. The process is meticulous. First, a weighing system measures out a precise quantity of raw beads, which are then fed into the expansion chamber. The chamber is sealed, and steam is introduced. Here, a Programmable Logic Controller (PLC) takes over, managing the steam valve to maintain the exact temperature and pressure for a specific duration, as defined by the "recipe" for the target density.
After the main expansion phase, the expanded beads are agitated and cooled slightly before an automated discharge system opens, and the fresh beads are pneumatically conveyed out of the chamber. This cycle—load, steam, expand, discharge—repeats. This method allows for incredibly tight control over the final density, often with a tolerance of less than 1%. For a business that produces a variety of eps products for different clients, each with unique specifications, the ability to quickly and reliably switch from producing a 12 kg/m³ eps batch to a 30 kg/m³ batch is a massive competitive advantage. These batch pre-expanders are the workhorses for versatile EPS manufacturers.
What are the Main Advantages of a Continuous Pre-Expander?
When your business model is built on massive scale and efficiency, the continuous pre-expander is the engine that drives your production process. Unlike its batch counterpart, the continuous eps pre-expander is designed for non-stop, high-volume output. Raw material is fed into the machine by a screw conveyor at a constant, adjustable rate. Inside the long, typically vertical expansion chamber, the beads are exposed to a steady flow of steam as they travel through the machine. By the time they exit at the bottom, they are fully expanded to the target density.
The primary benefit is sheer production capacity. A high-capacity continuous pre expander can process several tons of material per hour, making it the cornerstone of any large-scale eps production facility, especially those specializing in commodity products like insulation sheets. The process is highly automated, requiring minimal operator intervention once the parameters are set. This leads to lower labor costs per kilogram of product and exceptionally consistent product quality over long production runs. For a company aiming to be a market leader in styrofoam insulation, the economic advantages and production efficiency of a continuous pre-expander machine are undeniable.
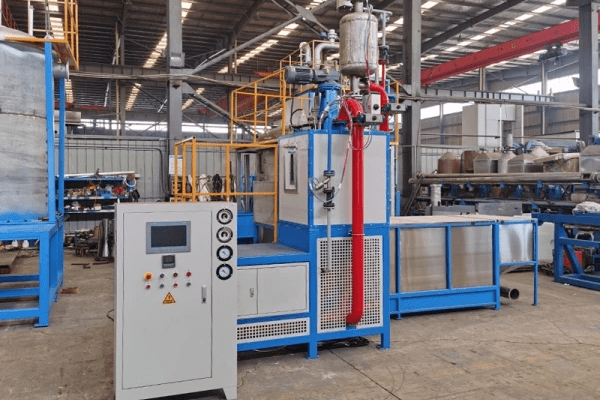
Choosing the Right EPS Pre-Expander: Which Model Fits Your Production Needs?
As a business owner, I know that choosing the right equipment is one of the most impactful decisions you’ll make. It’s not about which pre-expander machine is "better," but which one is better for you. To make the right choice, you need to ask yourself a few honest questions about your operation:
- What is your required production volume? Be realistic about your current and projected output. A continuous machine might seem appealing, but if your orders don’t justify its capacity, it will be underutilized. Conversely, trying to meet high-volume demand with a batch machine can lead to production bottlenecks.
- How diverse is your product range? If you are a one-stop shop for packaging, insulation, and custom shapes, you’ll need to change densities frequently. The flexibility of a batch EPS Pre-expander Machine is built for this. If 90% of your business is making one type of insulation board, a continuous model is far more efficient.
- What is your budget for capital investment and operation? Continuous machines often have a higher initial cost but can offer a lower operational cost per kilogram at high volumes due to higher automation and lower energy consumption per unit.
- How important is density precision? While both machine types are accurate, batch pre-expander systems are generally recognized for offering the highest level of precise control, which can be critical for high-specification technical parts.
By answering these questions, you can create a clear profile of your eps production needs and confidently select the machine that will serve as the most profitable asset for your company.
What Key Parameters Should You Monitor in an Expander Machine for Optimal Performance?
Operating an expander machine effectively is a science. To achieve consistent, high-quality results and ensure optimal performance, you must monitor and control several key parameters. Modern machines make this easier with integrated sensors and user-friendly control panels, but understanding what you’re controlling is essential. The most critical parameter is steam. You need to control not just the pressure, but also the quality (dryness) of the steam entering the chamber.
Beyond steam, you must manage the material feed. In a batch pre-expander machine, this is the weight of the charge. An integrated electronic scale ensures each batch starts with the exact same amount of raw material. In a continuous machine, it’s the speed of the feeding screw. Another critical factor is the level sensor inside the chamber, which maintains a consistent volume of beads during expansion. Advanced control systems on a modern EPS pre-expander machine will allow you to set, monitor, and adjust these variables digitally, often through a touchscreen interface. This level of precise control is what separates an average result from a perfect one, maximizing material usage and ensuring every consistent bead contributes to a superior final product.
How Do Modern EPS Pre-Expander Machines Enhance Production Efficiency and Safety?
The evolution of the EPS machine has been remarkable. Today’s models are not just more powerful; they are smarter, safer, and far more efficient. As a manufacturer, we’ve focused on integrating technology that directly addresses the pain points of production managers. One of the biggest advancements is the widespread adoption of the PLC (Programmable Logic Controller). This computer brain allows you to automate nearly the entire pre-expansion process. With a PLC, you can save specific "recipes" for different densities, ensuring perfect repeatability with the touch of a button.
From a construction standpoint, look for features like chambers and fluid bed dryers that are made of stainless steel. This not only prevents rust from contaminating your pristine white beads but also guarantees the longevity and durability of the machinery. For efficiency, features like automatic material feeding from a main hopper and pneumatic conveying to the silo reduce labor requirements and create a seamless workflow. Safety is also paramount. Modern machines are equipped with pressure relief valves, emergency stop systems, and robust safety guards, ensuring they meet international standards like CE certification, giving you peace of mind and protecting your most valuable asset: your people.
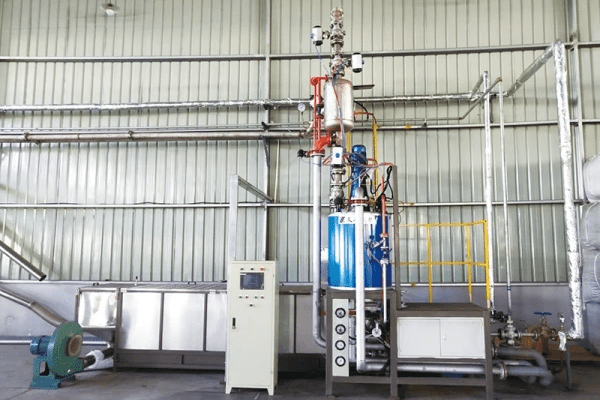
Beyond the Machine: The Importance of Upstream and Downstream Equipment
A successful eps production line is more than just a collection of different machines; it’s an integrated system where each component works in harmony. Your pre-expander machine is the heart, but it needs a strong circulatory system to function at its peak. Upstream, this means a reliable steam boiler capable of providing consistent, dry steam and a robust compressed air system for the pneumatic controls and conveying.
Downstream equipment is just as critical. Once the hot, moist beads exit the expander, they are typically sent to a fluid bed dryer for air cooling and drying. From there, they are conveyed to a large EPS Silo. This is not just a storage container; it’s an aging chamber. The freshly expanded beads need to rest in the silo for several hours (from 4 to 24 hours depending on density) to cool down completely and allow the internal pressure within each bead to stabilize. Skipping or shortening this aging process is a common mistake that leads to poor fusion during molding. Finally, an automated conveying system is needed to transport the aged beads from the silos to your Automatic EPS Block Conveyor and molding machines. Viewing your production as a complete process, not just a single machine, is key to maximizing efficiency and quality.
What Should You Look for in a Professional EPS Machine Manufacturer?
Choosing a supplier is as important as choosing the right machine. As a business owner myself, I understand that you’re not just buying steel and electronics; you’re investing in a partnership that should support your growth. Your relationship with a supplier can be the difference between seamless operation and constant headaches.
"As a machine manufacturer with decades of experience, I’ve learned that our relationship with a client doesn’t end at the sale. It begins. True partnership is built on reliability, support, and a deep understanding of their production goals." – Allen, YouLi Machinery
Here are the non-negotiables to look for in a professional EPS partner:
- Clear Communication: Can you have a clear, technical conversation with their team? Inefficient communication is a major pain point and can lead to costly misunderstandings.
- Proven Expertise: Do they understand your entire production process? A great supplier can advise you on how their pre-expander will integrate with your existing molding machines and recycling systems, like an EPS Recycling Machine.
- After-Sales Support: This is critical. Ask about their installation, training, and warranty policies. What happens when you need help? A reliable partner offers remote technical support and can dispatch engineers if needed.
- Spare Parts Availability: A machine is only as good as its weakest component. How quickly can they supply you with critical spare parts? Extended downtime waiting for a replacement part can be devastating to your bottom line. Look for a supplier who maintains a comprehensive inventory.
- Credibility and References: Don’t be afraid to ask for case studies or references from customers in your region, whether it’s the USA, Europe, or Australia. A confident manufacturer will be proud to share their success stories.
Key Takeaways to Remember
Making the right choice in an EPS pre-expander is a foundational decision for your business. Here are the most important points to remember:
- The Pre-Expander is Critical: The quality of your final EPS products is determined at the very first stage of pre-expansion.
- Batch for Flexibility: Choose a Batch Pre-Expander if your business thrives on producing a diverse range of products with different densities. It offers unmatched precision and control.
- Continuous for Capacity: Opt for a Continuous Pre-Expander if your goal is high-volume, efficient production of a single, consistent product like insulation panels.
- Look at the Whole System: Your pre-expander machine is part of a larger production line. Ensure your upstream (steam) and downstream (silos, conveying) equipment can support it.
- Modern Features Matter: Invest in machines with PLCs, stainless steel construction, and robust safety features. They increase efficiency, ensure longevity, and protect your team.
- Choose a True Partner: Select a machine manufacturer who offers more than just a machine. Look for excellent communication, reliable after-sales support, and a deep understanding of your industry.
Post time: 07-16-2025