Expanded Polystyrene (EPS) is a remarkably versatile material found everywhere, from protective packaging to building insulation. But how are those intricate EPS shapes created? The answer lies in the sophisticated technology of the EPS Shape Molding Machine and the precise process of EPS molding. This article delves deep into the world of EPS shape moulding, exploring the machinery, the manufacturing process, the science behind polystyrene transformation, and why understanding this is crucial for manufacturers like yourself. Whether you’re considering investing in new equipment or optimizing your current production, this guide provides valuable insights from a manufacturer’s perspective.
1. What Exactly is EPS and Why is Shape Moulding Important?
Essential to grasp what EPS truly is before diving into the machinery. EPS, or Expanded Polystyrene, is a rigid, cellular plastic foam material derived from polystyrene. It starts as tiny, solid beads of polystyrene containing a blowing agent, typically pentane. When heated, these beads expand significantly, forming a lightweight but strong structure composed mostly of air (around 98%). This unique composition gives EPS its excellent insulating properties, shock absorption capabilities, and low weight.
Shape moulding is the specific manufacturing process used to create complex, three-dimensional EPS products directly from these expanded polystyrene beads. Unlike cutting shapes from a large EPS block, shape moulding allows for intricate designs, custom fits, and integrated features. This is vital for applications requiring precise dimensions, such as custom packaging inserts for electronics, automotive components, helmets, or specialized construction elements. The ability to precisely mold EPS into virtually any form makes it indispensable across numerous industries, offering tailored solutions with minimal waste.
The demand for custom EPS components continues to grow, driven by needs for better product protection, lighter components in automotive and aerospace, and more energy-efficient building insulation. Therefore, mastering the EPS shape moulding process and utilizing efficient EPS Shape Molding Machines is key for manufacturers aiming to meet market demands and maintain a competitive edge. It enables the production of high-volume, consistent quality EPS products efficiently.
2. How Does the EPS Molding Process Transform Raw Beads into Finished Products?
The transformation of tiny polystyrene beads into a finished EPS product involves a fascinating multi-stage molding process. It’s a carefully orchestrated sequence relying on heat (steam), pressure, and precise timing within the molding machine. Think of it as taking a small raw material bead and puffing it up, then precisely welding millions of these puffed beads together inside a specific mold.
The general workflow looks like this:
- Pre-expansion: The raw material (solid beads of polystyrene resin) is heated with steam in a pre-expander, causing the blowing agent (pentane) within each bead to vaporize and expand the bead significantly, reducing its density. This step determines the final density of the EPS.
- Intermediate Aging/Conditioning: The freshly expanded beads are porous and unstable. They are stored in large silos for a period (hours to days) to cool, stabilize pressure, and allow air to diffuse into the bead structure, replacing residual pentane. These aged beads are crucial for proper fusion.
- Molding: The conditioned expanded beads are pneumatically conveyed into the mold cavity of the EPS Shape Molding Machine. The mold is then closed securely.
- Steam Fusion: Steam is injected directly into the closed mold. This heat softens the expanded beads further and causes residual blowing agent and diffused air to expand, forcing the beads to fuse together and conform perfectly to the shape of the mold cavity.
- Cooling: After fusion, the mold must be rapidly cooled, usually using water or air circulated through channels within the mold. This allows the fused EPS part to solidify and become rigid enough to handle.
- Ejection: Once sufficiently cooled, the mold opens, and the finished EPS part is ejected, often assisted by ejector pins or air pressure.
This entire molding process, from filling the mold to ejecting the part, constitutes one production cycle. Modern EPS Shape Molding Machines are designed to perform these steps rapidly and automatically, enabling high production volumes.
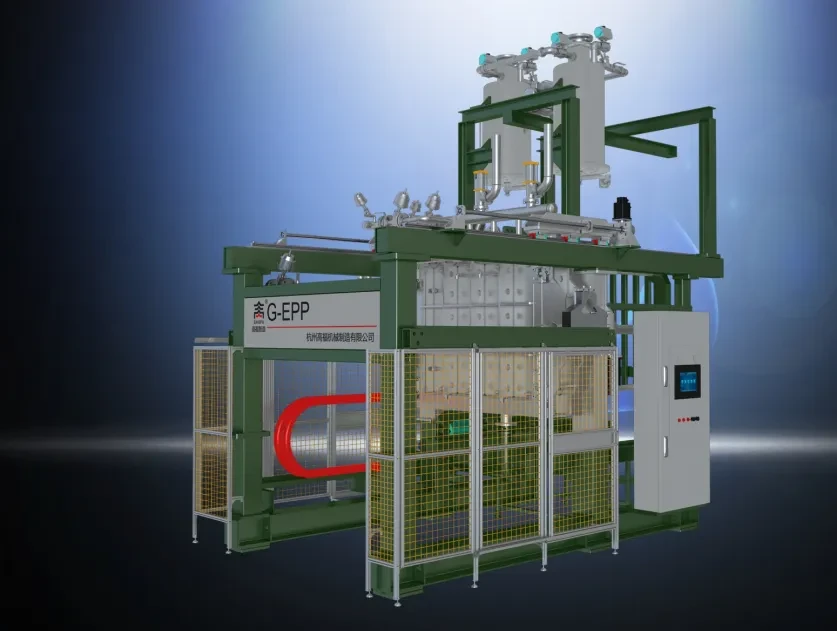
3. What is the Critical Role of Pre-expansion in the EPS Manufacturing Process?
Pre-expansion is arguably the most critical preparatory step in the entire EPS manufacturing process. It’s where the fundamental characteristic of EPS – its low density – is established. Without proper pre-expansion, achieving the desired lightweight properties, insulation value, and cushioning performance of the final EPS product is impossible. This stage directly impacts material consumption and final product quality.
During pre-expansion, the raw material (beads of polystyrene containing pentane) is fed into a specialized machine called an EPS Pre-expander machine. Inside, controlled steam heats the beads. The heat causes the polystyrene polymer to soften and the pentane blowing agent trapped inside each bead to vaporize. This internal pressure inflates the softened bead, much like popcorn kernels popping, increasing its volume by up to 50 times while significantly decreasing its density.
The degree of expansion, and thus the final density, is precisely controlled by regulating factors like steam pressure, heating time, and bead feed rate. Different applications require different EPS densities – lower densities for general packaging, higher densities for structural components or high-impact protection. Achieving the target desired density consistently during pre-expansion is vital for ensuring the final EPS parts meet performance specifications and minimizing material costs. An efficient pre-expander ensures uniform bead expansion, which is essential for consistent fusion in the subsequent molding process.
4. Inside the EPS Shape Molding Machine: How Does it Work?
The EPS Shape Molding Machine is the heart of the shape moulding operation. It’s a complex piece of equipment designed to automatically perform the filling, steaming, cooling, and ejection steps of the molding process with high precision and speed. While designs vary, most EPS Shape Molding Machines share core components and operational principles.
Key components typically include:
- Machine Frame: Provides the structural support for all components.
- Mold Clamping System: Usually hydraulic or electro-mechanical, this system securely closes and holds the two halves of the mold together against the significant pressure generated during steam injection.
- Filling System: Uses injectors or filling guns connected to a pressurized hopper to rapidly fill the mold cavity with the pre-expanded EPS beads.
- Steam System: A network of pipes, valves, and chambers to inject controlled steam into the mold for bead fusion. Precise control over steam pressure and duration is critical.
- Cooling System: Incorporates channels within the mold plates and connections for circulating cooling water or air to rapidly reduce the mold temperature after steaming. An efficient cooling system shortens cycle times.
- Vacuum System (Optional but common): Often used to assist filling (drawing beads into complex mold areas) and enhance cooling/drying by drawing residual moisture and heat from the mold.
- Ejection System: Pins or air jets that push the finished EPS part out of the mold once it opens.
- Control System (PLC): The brain of the eps machine, typically a Programmable Logic Controller (PLC) with a user interface (HMI), manages all sequences, timings, pressures, and temperatures for automated production cycles.
In operation, the PLC orchestrates the sequence: the mold closes, beads are injected, steam is applied for a set time, the cooling cycle runs, the mold opens, and the part is ejected. This cycle repeats continuously, allowing for high-volume production of identical EPS parts. Modern machines emphasize energy efficiency, rapid cycle times, and user-friendly controls.
5. The Science of Steam: How Does it Fuse EPS Beads in the Mold?
Steam is the magic ingredient in the EPS molding process. Its ability to transfer heat rapidly and efficiently is perfectly suited for fusing the pre-expanded EPS beads together within the confines of the mold. Understanding how steam heating works is key to appreciating the EPS molding technology.
When steam is injected into the closed mold filled with expanded beads, several things happen simultaneously:
- Heat Transfer: The hot steam (typically around 100-120°C or 212-248°F, depending on pressure) condenses on the cooler surfaces of the beads. This condensation releases a significant amount of latent heat directly onto the bead surface, causing the polystyrene to soften quickly and uniformly.
- Further Expansion: The heat also causes any residual blowing agent (pentane) and the air that diffused into the beads during aging to expand further.
- Fusion: As the beads soften and expand, they press tightly against each other within the fixed volume of the mold cavity. The softened surfaces merge and fuse together at the points of contact, creating a monolithic structure that replicates the internal shape of the mold.
The pressure and duration of the steam injection are critical parameters. Insufficient steam results in poor fusion and weak parts. Excessive steam can cause the EPS structure to collapse or lead to overly long cooling times. The molding machine‘s control system precisely regulates the steam cycle to ensure complete and efficient fusion, resulting in strong, well-formed EPS products with the desired density. The effectiveness of the steam penetration also depends on the quality and consistency of the pre-expansion and aging steps.
6. Why is the Cooling Phase Essential for EPS Product Quality?
While steam fusion creates the EPS part, the cooling process is equally critical for achieving final product quality, dimensional stability, and efficient production. Immediately after steam injection, the newly fused EPS part is hot, soft, and contains residual internal pressure. Attempting to eject it from the mold at this stage would lead to deformation, shrinkage, or even collapse.
The cooling phase serves several vital purposes:
- Solidification: Cooling rapidly reduces the temperature of the EPS material, causing the softened polystyrene to transition back to a rigid, solid state. This gives the part the structural integrity needed to withstand ejection and handling.
- Pressure Reduction: As the part cools, the internal pressure from expanded gases (air and residual pentane) decreases. This prevents the part from warping or expanding uncontrollably after being removed from the mold.
- Dimensional Stability: Proper cooling ensures the EPS part retains the exact shapes and sizes imparted by the mold cavity, minimizing post-molding shrinkage or distortion.
- Cycle Time Reduction: An efficient cooling system, often using chilled air or water circulated through integrated channels in the mold plates, removes heat quickly. Faster cooling means shorter overall cycle times, leading to higher productivity from the molding machine. Vacuum assistance can further accelerate cooling and drying.
The duration of the cooling cycle must be carefully balanced. It needs to be long enough to ensure the part is sufficiently rigid and stable but short enough to maximize production throughput. Factors influencing cooling time include part thickness, EPS density, mold temperature, and the efficiency of the machine’s cooling system. Consistent and controlled cooling is paramount for producing high-quality, dimensionally accurate EPS parts.
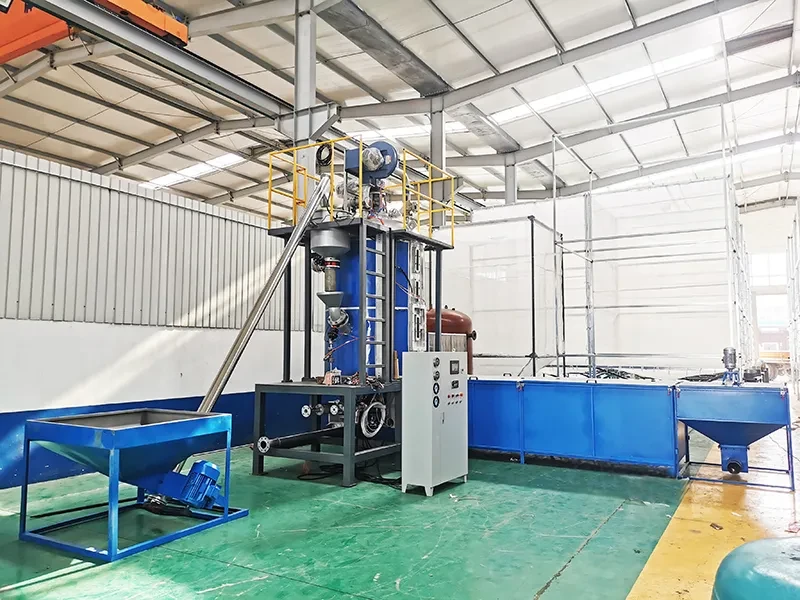
7. Exploring Different Types of Molds Used in EPS Shape Moulding
The mold (or mould) is the component that defines the final shape of the EPS product. It’s essentially a custom-made tool, typically constructed from aluminum alloy due to its excellent thermal conductivity (for both heating and cooling) and ease of machining. The quality and design of the mold directly impact product quality, surface finish, and production efficiency.
EPS molds consist of at least two halves: a fixed half and a moving half, mounted onto the platens of the EPS Shape Molding Machine. The internal surfaces form the mold cavity, which is the negative image of the desired part. Several features are incorporated into EPS mold design:
- Fill Injectors: strategically placed openings where the expanded beads enter the mold cavity.
- Steam Vents/Chambers: Small holes or specialized core vents that allow steam to enter the cavity uniformly and air to escape during filling and steaming. They are designed to let gases pass but retain the EPS beads.
- Cooling Channels: Internal passages machined into the mold plates through which cooling water or air circulates to remove heat efficiently.
- Ejector Pins: Activated when the mold opens to push the finished part out.
- Surface Finish: The cavity surface can be polished, textured, or incorporate logos and text as required for the final EPS product.
- Mold Material: Primarily aluminum alloys (like Alumec or Hokotol) for good heat transfer and machinability. Sometimes steel inserts are used for high-wear areas or complex features within the mold.
Molds can range from simple two-plate designs for basic shapes to complex multi-cavity molds for producing several parts per cycle, or intricate molds with slides and cores for complex geometries. The precision engineering of the mold, including venting, cooling channel layout, and sealing surfaces, is crucial for achieving consistent part quality, minimizing defects, and optimizing cycle times in the EPS molding process. Investing in high-quality, well-designed molds is essential for any serious EPS foam manufacturer.
8. What are the Diverse Applications of EPS Molded Parts?
The versatility, lightweight nature, insulation properties, and shock absorption capabilities of EPS foam, combined with the precision of the shape moulding process, make it suitable for an incredibly wide range of applications of EPS. The ability to create custom shapes and sizes efficiently opens up possibilities across many sectors.
Some key application areas include:
- Protective Packaging: This is perhaps the most well-known use. Custom-molded EPS inserts provide superior protection for fragile goods like electronics (TVs, computers), appliances (refrigerators, washing machines), medical equipment, and glassware during shipping and handling. Its lightweight nature also reduces transport costs.
- Building and Construction: EPS is widely used for thermal insulation in walls, roofs, and floors (insulation boards). Molded EPS can also be used for insulated concrete forms (ICFs), architectural moldings, void fillers, and geofoam for lightweight structural fill in civil engineering projects. Check out our Vertical EPS Block Moulding Machine for producing insulation blocks.
- Automotive Components: Used for interior impact absorption (e.g., in bumpers), sound dampening, lightweight fillers, and components like sun visors and tool kits. EPP (Expanded Polypropylene), a related material often processed on similar machinery, is also prevalent here.
- Appliances: Found inside refrigerators, air conditioners, and other appliances as thermal insulation components.
- Horticulture: Seedling trays and propagation containers.
- Safety Equipment: Inner liners for helmets (bicycle, motorcycle, industrial).
- Floatation: Buoys, life vests, and floating docks.
- Consumer Goods: Coolers/ice boxes, decorative items, model making.
The list is constantly expanding as designers and engineers find new ways to leverage the unique properties of molded EPS. The efficiency of the EPS shape moulding process allows for cost-effective production of both high-volume standard parts and specialized custom components.
9. Choosing the Right EPS Shape Molding Machine: Key Factors for Buyers
Selecting the appropriate EPS Shape Molding Machine is a critical investment decision for any EPS manufacturer, impacting productivity, product quality, operational costs, and future capabilities. For buyers like Mark Thompson, focusing on performance, reliability, and support is paramount. As a manufacturer (Allen from YouLi), we understand these concerns deeply.
Here are key factors to consider:
- Machine Size and Platen Dimensions: Must accommodate the largest mold size you anticipate using. Consider both current needs and potential future products.
- Production Capacity & Cycle Times: Evaluate the machine’s rated output based on typical cycle times for parts similar to yours. Faster cycle times mean higher throughput. Look for efficient steam and cooling systems.
- Automation Level: Modern machines offer high degrees of automation, reducing labor costs and improving consistency. Features like automatic mold changing, robotic part removal, and integrated process monitoring are valuable.
- Energy Efficiency: Steam and electricity consumption are significant operational costs. Look for machines with energy-saving features, such as optimized steam control, efficient vacuum systems, and well-insulated steam chambers.
- Control System: A user-friendly PLC/HMI interface with precise control over all molding process parameters (steam time/pressure, cooling time, filling parameters) is essential for consistent quality. Data logging and remote diagnostics are beneficial.
- Build Quality and Reliability: Opt for machines built with high-quality components (hydraulics, pneumatics, controls) from reputable brands. Robust construction ensures longevity and minimizes downtime. Ask about warranty and component sourcing.
- Mold Compatibility: Ensure the machine’s clamping system, ejector pattern, and utility connections (steam, water, air, vacuum) are compatible with your existing or planned molds.
- Supplier Reputation and Support: This is crucial. Choose a supplier with a proven track record, responsive technical support, readily available spare parts, and comprehensive training programs. Address Mark’s pain points: clear communication, on-time delivery, installation support, and reliable after-sales service are non-negotiable. Our range of EPS Shape Moulding Machines are designed with these factors in mind.
- Safety Features: Ensure the machine complies with international safety standards (e.g., CE marking) and includes necessary guards, interlocks, and emergency stops.
Carefully evaluating these factors against your specific production requirements and budget will help you select an EPS Shape Molding Machine that delivers reliable performance and a strong return on investment.
10. How Can Regular Maintenance Ensure Peak Performance of Your EPS Molding Machine?
Investing in a high-quality EPS Shape Molding Machine is just the first step. Ensuring its long-term reliability and peak performance requires a commitment to regular maintenance. Neglecting maintenance can lead to inconsistent product quality, increased downtime, higher energy consumption, and potentially costly repairs – directly impacting your bottom line and addressing common pain points for operators.
A proactive maintenance schedule should include:
- Daily Checks: Inspecting for leaks (steam, water, air, hydraulic fluid), checking safety guards and emergency stops, monitoring operating pressures and temperatures, and ensuring the mold area is clean.
- Weekly Maintenance: Lubricating moving parts (e.g., tie bars, ejector system), cleaning filters (air, water, vacuum), checking mold vents for blockage, inspecting hoses and connections.
- Monthly/Quarterly Maintenance: More thorough inspection of hydraulic systems, checking electrical connections, calibrating sensors (temperature, pressure), inspecting the mold clamping mechanism, verifying steam trap function, and cleaning cooling channels within the mold and machine.
- Annual Maintenance: Comprehensive inspection and overhaul as recommended by the manufacturer, potentially including seal replacements, hydraulic fluid change, and detailed system diagnostics.
- Mold Maintenance: Regularly cleaning mold surfaces and vents is crucial. Blocked vents can cause filling issues and poor fusion. Damaged mold surfaces affect part finish. Proper mold storage is also important.
Maintaining a logbook of all maintenance activities is essential. Furthermore, ensuring operators are properly trained not only on machine operation but also on basic maintenance checks can prevent minor issues from escalating. Partnering with a supplier like YouLi, who provides clear maintenance guidelines and responsive support for parts and service, is vital for keeping your EPS molding operations running smoothly and efficiently. Addressing concerns about spare parts availability proactively is key.
11. The Future Outlook for EPS Foam and Molding Technology
The future for EPS foam and the molding technologies that produce it looks bright, driven by ongoing innovation and market trends. While facing competition from other materials and increasing environmental scrutiny, EPS‘s core benefits – lightweight, excellent insulation, cost-effectiveness, and recyclability – ensure its continued relevance. Technology advances in EPS molding machines and processes are further strengthening its position.
Key trends shaping the future include:
- Enhanced Sustainability: Increased focus on recyclable EPS and closed-loop systems. Development of EPS grades with bio-based content. Improved EPS recycling infrastructure and technologies, such as our EPS Recycling Machine EPS Crusher + De-duster+ Dust compactor, play a vital role.
- Increased Automation and Industry 4.0: Integration of robotics for part handling, automatic mold changing systems, and smart controls with real-time process monitoring, data analytics, and predictive maintenance capabilities to optimize efficiency and quality.
- Improved Energy Efficiency: Continuous development of molding machines with reduced steam and energy consumption through better insulation, optimized steam delivery, and more efficient cooling and vacuum systems.
- Material Advancements: Development of specialized EPS grades with enhanced properties (e.g., higher thermal resistance, improved fire retardancy, greater strength). Growing use of EPP and other expandable polymers processed on similar machinery platforms.
- Faster Cycle Times: Ongoing refinements in machine design, mold technology (expansion and cooling strategies), and control systems to further reduce production cycles and increase output.
- Precision and Complexity: Ability to mold more intricate parts with thinner walls and tighter tolerances, expanding applications of EPS into new areas.
As a manufacturer dedicated to this industry, YouLi is committed to incorporating these advancements into our EPS machines. We believe that by embracing innovation and focusing on efficiency and sustainability, the EPS molding industry will continue to thrive, providing essential products for packaging, construction, and countless other applications. Understanding the nuances of the expansion and fusion process of EPS remains fundamental to leveraging these future opportunities.
Key Takeaways: EPS Shape Moulding Essentials
- EPS (Expanded Polystyrene) is a lightweight, insulating foam created by expanding and fusing polystyrene beads.
- Shape moulding uses a specialized molding machine and custom molds to create complex 3D EPS parts directly from expanded beads.
- The molding process involves Pre-expansion, Aging, Mold Filling, Steam Fusion, Cooling, and Ejection.
- Pre-expansion controls the final density of the EPS foam.
- The EPS Shape Molding Machine automates the process using precise control of steam, cooling, and mechanics.
- Steam provides the heat necessary to soften and fuse the expanded polystyrene beads within the mold cavity.
- Efficient cooling is crucial for part solidification, dimensional stability, and short cycle times.
- High-quality aluminum molds with well-designed cavities, vents, and cooling channels are vital for product quality.
- EPS has diverse applications, especially in protective packaging and building insulation.
- Choosing the right molding machine involves considering size, capacity, automation, energy efficiency, controls, reliability, and supplier support.
- Regular maintenance of both the eps machine and the mold is essential for consistent performance and longevity.
- The future of EPS molding involves greater sustainability, automation, efficiency, and material innovation.
Post time: 04-21-2025