Expanded Polystyrene (EPS), commonly known by the brand name Styrofoam, is everywhere. It’s the protective packaging for your new appliance, the insulation in construction, and the disposable cup for your coffee. But its lightweight, bulky nature creates a massive waste management challenge. As a business owner in the EPS or EPP industry, you see this firsthand. You’re likely dealing with mountains of scrap, facing high disposal costs, and looking for a more sustainable and profitable solution. This is where a dedicated EPS recycling machine becomes not just an environmental choice, but a smart business decision.
This article is for decision-makers like you. I’m Allen, and my factory in China has been manufacturing EPS and EPP foam machinery for decades. I’ve spoken with hundreds of company owners and procurement officers, like Mark Thompson from the USA, who are decisive, quality-sensitive, and looking for the best value. I understand your concerns—performance, reliability, and support are paramount. This guide will walk you through everything you need to know about EPS foam recycling technology, drawing on my first-hand experience to help you turn your Styrofoam waste into a valuable asset.
What Exactly is Expanded Polystyrene (EPS) and Why Does it Need a Special Recycling Machine?
Expanded Polystyrene (EPS) is a rigid cellular plastic foam material derived from petroleum. The magic of EPS is that it’s composed of about 98% air, trapped within a closed-cell structure of polystyrene. This makes it an incredibly lightweight and effective insulator, perfect for packaging, construction, and more. However, this very quality is what makes it a recycling nightmare. The sheer bulk of EPS foam means it takes up a disproportionate amount of space in trucks and landfills. Transporting light, airy foam to a recycling facility is often not economically viable.
This is why a specialized recycling machine is essential. You can’t just toss Styrofoam scrap into a standard plastic recycler. A dedicated machine for recycling EPS is engineered to tackle the core problem: volume. By dramatically reducing the volume of the foam, these machines transform a logistical and financial burden into a manageable, and even profitable, commodity. The goal is to remove the air and densify the polystyrene into a compact form that is easy to store, transport, and sell.
From my experience in this business, I’ve seen companies completely overhaul their waste management strategy with one piece of equipment. They go from paying fees to dispose of EPS waste to generating a new revenue stream. The right machine is the critical first step in making EPS a truly recyclable part of the circular economy.
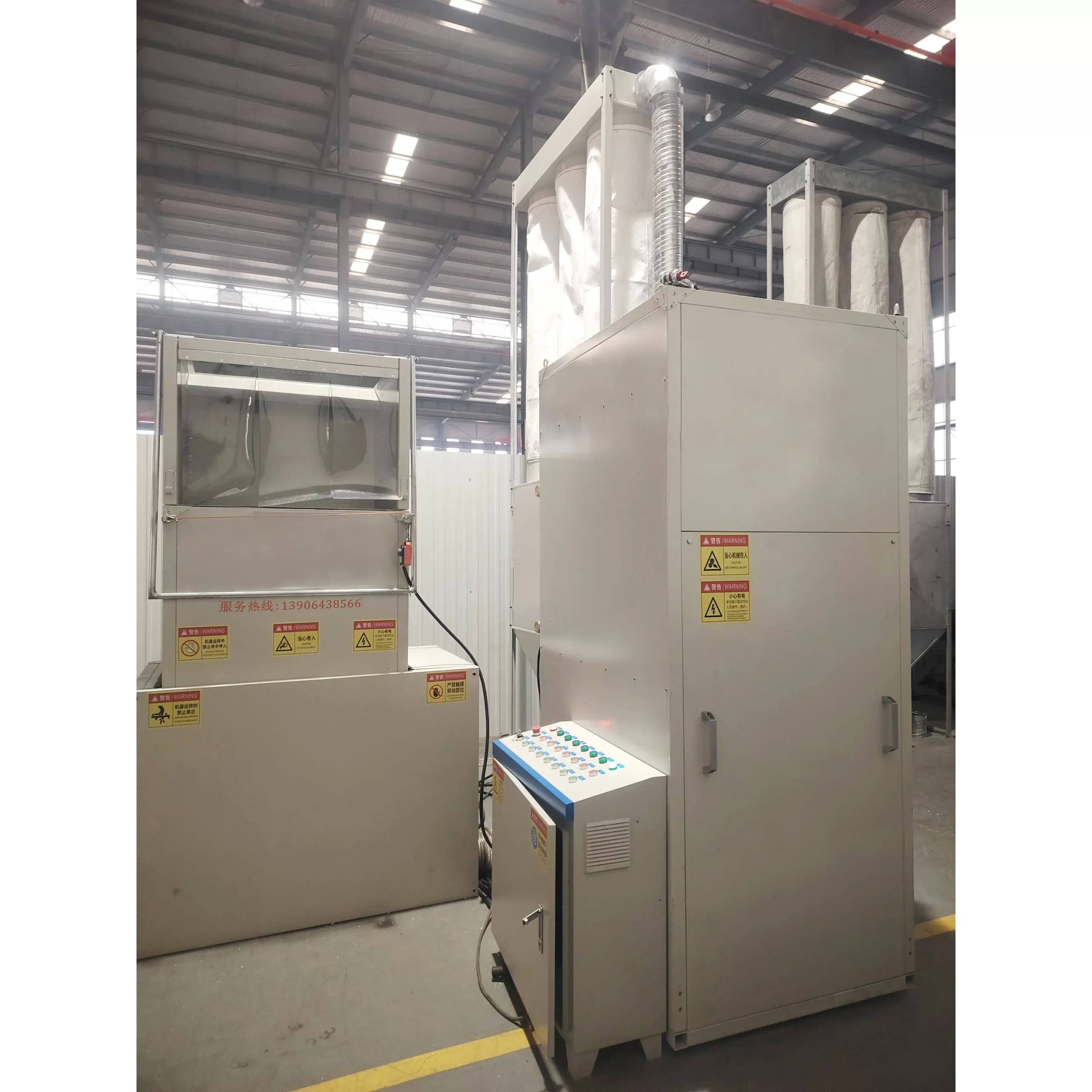
How Does an EPS Foam Densifier Work to Reduce Volume?
The term "foam densifier" sounds technical, but the concept is straightforward. An EPS foam densifier is a machine designed to crush EPS foam and compact it into dense, solid blocks or ingots. The primary function is to reduce the volume of the foam material, often achieving an incredible compaction ratio of up to 90:1. Imagine ninety truckloads of loose foam scrap being condensed into a single truckload of densified polystyrene. That’s the power of this technology.
There are two main methods a densifier uses: cold compaction and hot melting. In a cold compactor, the foam is fed into the machine, shredded into smaller pieces, and then forced through a chamber by a powerful screw. The pressure exerted by the screw compresses the foam, squeezing out the air and forming a continuous, dense log or block. This process doesn’t require significant heating.
A hot melting machine, on the other hand, uses thermal energy. The foam is shredded and then exposed to controlled heat, which causes it to melt without burning. The molten polystyrene is then extruded through a die, where it cools and solidifies into a highly dense, plastic-like ingot. Both methods effectively reduce the volume, but the final product and operational requirements differ, which we’ll explore next.
What Are the Key Differences Between a Styrofoam Compactor and a Hot Melting Machine?
Choosing between a Styrofoam compactor (cold press) and a hot melting machine (thermal densifier) is a key decision for any business owner. Both machines recycle Styrofoam, but they do it differently, and the right choice depends on your specific needs, like operational capacity and the desired end-product.
A Styrofoam compactor, often called a cold compactor, uses immense physical pressure. Think of it as a giant, powerful garlic press for foam. The key benefit is lower energy consumption since it doesn’t rely on heating elements. The resulting densified block is solid, but typically has a lower density than what a hot melt machine produces. This process is generally simpler and can be a very cost-effective solution for many operations.
In contrast, an EPS Hot Melt Machine uses a thermal process. It melts the Styrofoam into a taffy-like consistency before extruding it. This method produces a much denser, almost glass-like ingot that is often considered a higher-quality raw material by downstream processors. The hot melting process can also handle slightly more contamination. The trade-off is higher energy usage and a more complex piece of equipment.
Here’s a simple table to summarize the key differences:
Feature | EPS Compactor Machine (Cold Press) | EPS Hot Melting Machine (Thermal) |
---|---|---|
Process | Mechanical pressure via a screw | Thermal melting and extrusion |
Energy Use | Lower | Higher |
Final Product | Dense blocks (compresses log) | Very dense ingots (molten extrudate) |
Density | Good (e.g., 200-250 kg/m³) | Excellent (e.g., 600-700 kg/m³) |
Footprint | Generally smaller | Can be larger due to heating/cooling |
Ideal For | Businesses seeking a low-energy, straightforward solution | Operations prioritizing max density and end-product value |
As a manufacturer, we produce both types because we understand that our customers have different priorities. An EPS Compactor Machine is an excellent entry point into foam recycling, while an eps hot melting machine is for those looking to maximize the value of their recycled material.
Can You Recycle All Types of Foam with One Machine? (EPS, XPS, EPP)
This is a question I get often, especially at exhibitions. Business owners want a versatile solution. The simple answer is: not always. Most foam recycling machines are optimized for a specific type of foam. The three most common types are:
- EPS (Expanded Polystyrene): The white, beaded foam used in packaging and disposable cups. This is the most common material these machines are designed for.
- XPS (Extruded Polystyrene): A rigid, often colored (pink or blue) foam board used for building insulation. It has a more uniform cell structure than EPS.
- EPP (Expanded Polypropylene): A more flexible and durable foam that has a "memory" and can return to its shape. It’s common in automotive parts like bumpers and reusable industrial packaging.
While an EPS recycling machine is perfect for Styrofoam, processing XPS or EPP often requires different parameters. XPS has a different melting point and density, and EPP is a completely different polymer (polypropylene, not polystyrene). Some advanced machines offer the capability to handle different types of foam, but it’s crucial to confirm this with the manufacturer. Trying to recycle the wrong foam material in a standard machine can lead to poor results, damage the equipment, or even create a safety hazard. Always be clear about the types of foam you need to process when discussing your needs.
What’s the Process for Turning Waste Styrofoam into a Valuable Material?
The journey from a pile of Styrofoam scrap to a valuable commodity is a streamlined process with the right equipment. It’s a transformation that my customers find incredibly rewarding. The process generally follows four key steps, creating a mini production line for recycling.
- Collection & Sorting: The first step is gathering the EPS waste. This includes cutting scraps from production, used packaging, and other sources. It’s important to sort out any significant contaminants like cardboard, food waste, or other plastics at this stage. A cleaner input leads to a better output.
- Crushing/Shredding: The bulky foam pieces are fed into a crusher or shredder. This breaks the foam down into smaller, more manageable "fluff." This step is crucial for ensuring the material feeds smoothly and consistently into the densification stage.
- Densification (Compaction or Melting): This is the core of the process. The shredded foam is fed into either a cold compactor or a hot melting machine. The machine works to extrude a dense log or ingot, removing the air and creating a solid polystyrene foam block.
- Cooling & Palletizing: The densified polystyrene exits the machine and is cut to length. After cooling, these blocks or ingots are stacked on pallets. They are now a stable, compact, and valuable raw material, ready to be sold to manufacturers who will use them for pelletizing and creating new plastic products like picture frames, park benches, and even new insulation.
This entire operation turns what was once a costly waste stream into a new product, closing the loop and contributing to a more sustainable model.
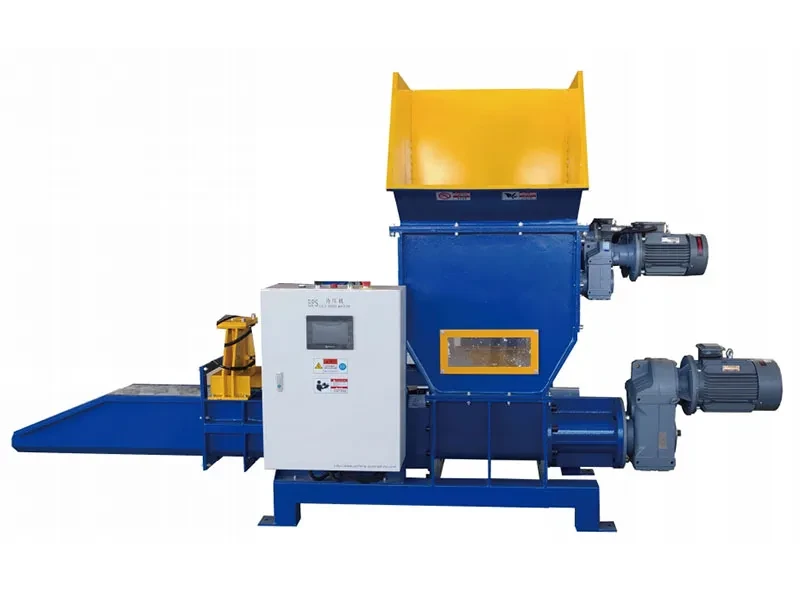
How Does an EPS Recycling Machine Benefit Your Business’s Bottom Line?
As a business owner, your decisions are driven by efficiency and profitability. Investing in an EPS recycling machine is not just an environmental decision; it’s a financial one. From my conversations with clients like Mark, the return on investment is a critical factor. The benefits are clear and measurable.
First, you drastically cut costs. Think about your current expenses for Styrofoam waste disposal. Landfill fees, dumpster rentals, and transportation costs add up quickly. A foam densifier can reduce the volume of your foam waste by up to 90%. This means fewer dumpster pickups and significantly lower transportation bills. Some of our customers have eliminated their foam disposal costs entirely.
Second, you create a new revenue stream. The densified EPS blocks are a sought-after commodity. Manufacturers of recycled plastics pay good money for this clean, consistent raw material. Instead of paying to have your scrap hauled away, you can sell it. The market price for recycled polystyrene fluctuates, but it consistently provides a positive return, turning a liability into an asset.
Finally, there are the intangible benefits. A sustainable business practice is a powerful marketing tool. It enhances your brand’s reputation and can be a deciding factor for your own customers. It also improves workplace cleanliness and safety by efficiently managing scrap foam. The investment in a recycling machine pays for itself through savings, sales, and a stronger, greener brand.
"We used to have three large dumpsters just for our EPS scrap, picked up weekly. After installing a YouLi hot melt densifier, we fill one pallet with densified ingots every two weeks. Our disposal costs went to zero, and we now sell the ingots for a profit. The machine paid for itself in 18 months." – A satisfied customer in the furniture industry.
What Should You Look for When Choosing a Machine for Recycling EPS Foam?
When you’re ready to invest in a foam recycling machine, the options can seem overwhelming. As a procurement officer, you need to look past the sales pitch and focus on the factors that determine long-term value and reliability. Here are the key considerations I always discuss with potential buyers:
- Production Capacity: How much foam scrap do you generate? Be realistic about your daily or weekly volume. Choose a machine that can comfortably handle your peak load without being oversized and inefficient for your typical needs. We offer a wide range of models to match different outputs.
- Automation and Labor: How much manual intervention is required? A highly automated machine can reduce labor costs and ensure consistent operation. Look for features like automatic feeding, cutting, and control systems.
- Energy Consumption: This is especially important if you’re considering an eps hot melting machine. Ask for the power rating (kW) and compare the energy efficiency between different models. An energy-saving design will lower your operating costs over the life of the machine.
- Durability and Construction: A recycling machine is a workhorse. Inspect the build quality. Is the frame made of heavy-gauge steel? Are the components (motors, gearboxes, screws) from reputable brands? A well-built machine will last for years with proper maintenance.
- Safety Features: Your team’s safety is non-negotiable. The machine should have emergency stop buttons, safety guards over moving parts, and clear operational warnings. For hot melt systems, proper insulation and ventilation are critical.
- Footprint and Space: Do you have the physical space for the equipment? Get the dimensions of the machine and ensure it fits into your workflow. A space-saving design can be a significant benefit.
Considering these factors will help you select not just any machine, but the right machine for your business.
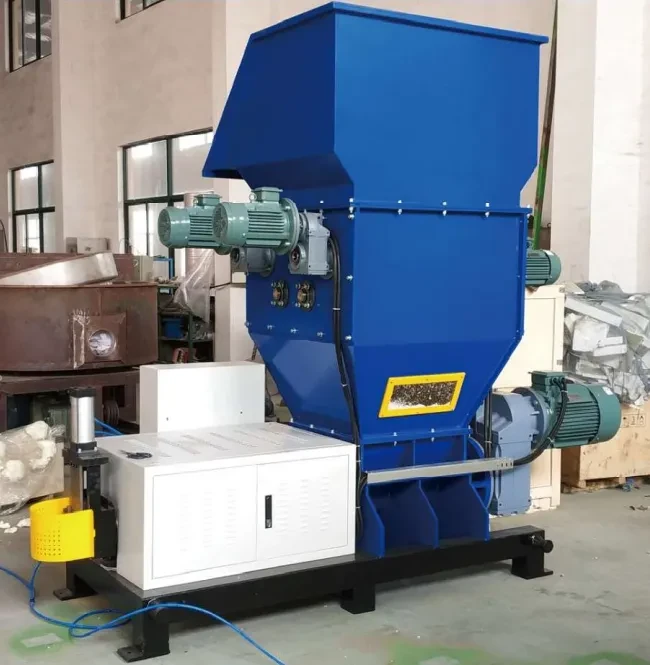
How Do You Handle Dirty or Contaminated EPS Waste Plastic?
This is a practical and important question. In the real world, waste foam isn’t always perfectly clean. It might have dust, labels, or other minor contaminants. The level of contamination will determine the best approach and the type of equipment you need. For lightly dirty EPS, a hot melt system can often be more forgiving than a cold compactor, as the heat can burn off some minor impurities.
For more significant contamination, especially dust and small particles from cutting operations, a more comprehensive solution is needed. This is where a complete recycling system comes into play. We’ve designed an integrated EPS Recycling Machine EPS Crusher + De-duster+ Dust compactor. This system works in three stages:
- Crusher: Breaks down the EPS blocks into small pieces.
- De-duster: Tumbles the crushed pieces to separate and remove loose dust and debris.
- Dust Compactor: Collects the fine dust and compacts it separately, keeping your main densified product clean and valuable.
This type of integrated system is ideal for high-volume producers who want to minimize waste and maximize the quality of their recycled polystyrene. It ensures that even waste plastic from a busy production floor can be processed efficiently, resulting in a cleaner final product that commands a higher price on the market.
Why is After-Sales Support Crucial for Your Foam Recycling Equipment?
As a customer, Mark’s biggest pain points often come after the purchase: delivery delays, poor training, and difficulty getting support. I can’t stress this enough: the quality of the machine is only half the equation. The quality of the manufacturer’s support is the other half. When you invest in a critical piece of equipment like a Styrofoam recycling machine, you are entering a long-term partnership with the supplier.
Downtime is lost revenue. If your machine breaks down, you need a responsive partner who can help you troubleshoot the problem quickly. Before you buy, ask these questions:
- What does your installation and training process look like?
- Do you have technical support staff who speak my language?
- How quickly can you ship spare parts?
- What is the warranty, and what does it cover?
At our company, we see after-sales service as a core part of our offering. We provide detailed manuals, remote video support, and a commitment to keeping a stock of critical spare parts. A reliable manufacturer doesn’t just sell you a machine; they provide the support to ensure that machine runs productively for its entire lifespan. This peace of mind is invaluable and a hallmark of a truly professional supplier.
What is the Future of Polystyrene Foam Recycling?
The future for polystyrene foam recycling is incredibly bright. For years, EPS was wrongly seen as unrecyclable by the public. Today, with growing environmental awareness and advanced recycling machine technology, that perception is changing. Governments, corporations, and consumers are all pushing for more sustainable solutions, and recycled polystyrene is a key part of that.
We’re seeing a shift towards a circular economy, where waste is designed out of the system. Investing in an EPS recycling machine positions your business at the forefront of this movement. The demand for high-quality recycled polystyrene pellets and ingots is growing as more companies commit to using recycled content in their foam products and packaging. The processing technology will continue to improve, becoming even more efficient and capable of handling a wider range of materials.
For a business owner, this means that an investment in foam recycling equipment today is not just a solution for a current problem; it’s a strategic move for the future. It aligns your operation with market trends, regulatory directions, and customer expectations. You’ll not only be running a more efficient and profitable business but also be a leader in the sustainable manufacture of polyethylene and polystyrene products.
Key Takeaways to Remember
As you consider your options, here are the most important points from my experience as a manufacturer and partner to businesses like yours:
- EPS is Highly Recyclable: With the right machine, Styrofoam waste can be transformed from a costly problem into a profitable product.
- Choose the Right Technology: Understand the difference between a cold compactor and a hot melting machine to select the best solution for your volume, budget, and end-product goals.
- Quality and Support Matter: Don’t just look at the price tag. Invest in a well-built machine from a manufacturer who provides excellent, reliable after-sales support.
- Financial Benefits are Real: Recycling EPS foam directly impacts your bottom line by eliminating disposal costs and creating a new revenue stream.
- It’s a Sustainable Future: Investing in foam recycling technology aligns your business with the global push for a circular economy, making your operation more resilient and respected.
Post time: 06-23-2025