Styrofoam, that lightweight, bulky material known technically as Expanded Polystyrene (EPS), is everywhere. It protects our new electronics, insulates our buildings, and keeps our food fresh. But for businesses, it often represents a significant waste management headache and a major expense. What if you could transform that bulky waste into a valuable, manageable resource? This article is your comprehensive guide to understanding Styrofoam recycling machines. We’ll explore how this technology works, the benefits it offers your business, and how to choose the perfect machine to turn your foam problem into a profitable solution.
What is Styrofoam and Why is it So Hard to Recycle?
First, let’s clarify what we mean by "Styrofoam." While Styrofoam™ is a brand name for a specific type of extruded polystyrene (XPS) insulation, the term is commonly used to describe Expanded Polystyrene, or EPS, foam. This is the white, beaded material you see in packaging, coolers, and disposable cups.
The biggest challenge with recycling Styrofoam is its composition. Believe it or not, EPS foam is about 98% air. This incredible lightness makes it an excellent insulator and cushioning material, but it also makes it extremely bulky. For businesses that generate a lot of EPS waste, this creates several problems:
- High Disposal Costs: Waste management companies often charge by volume, not weight. A dumpster full of uncompressed foam is mostly empty space, but you still pay a premium to have it hauled away.
- Inefficient Transport: Transporting lightweight, bulky waste is not cost-effective. It takes a massive truckload of loose Styrofoam to yield a small amount of actual polystyrene material, making traditional recycling methods economically unviable for many.
- Environmental Impact: When not properly managed, this material clogs landfills, where it takes centuries to break down. It can easily be broken into small pieces and contaminate waterways and ecosystems.
This is precisely the problem that a Styrofoam recycling machine is designed to solve. It tackles the volume issue head-on, making it feasible and profitable to recycle this useful plastic.
How Does a Styrofoam Recycling Machine Actually Work?
At its core, a Styrofoam recycling machine is designed to do one thing very effectively: remove the air. The basic process is remarkably straightforward and transforms a mountain of fluffy foam into a dense, manageable block or ingot.
Here’s a simplified breakdown of the journey your EPS waste takes inside one of these machines:
- Feeding: An operator places the loose Styrofoam pieces into the machine’s hopper. This can be done manually or via a conveyor system for higher-volume operations.
- Shredding/Crushing: High-torque blades or shredders break the large foam pieces into a smaller, more uniform size. This step is crucial for ensuring the material can be compacted evenly.
- Compaction: This is where the magic happens. The shredded polystyrene is forced through a chamber using a powerful hydraulic press or a screw mechanism. This immense pressure squeezes out all the air, compacting the material into a solid form.
- Extrusion: The highly compressed polystyrene is then pushed out of the machine as a continuous, dense block. This final product is solid, stackable, and easy to store and transport.
The entire operation is a continuous process, allowing a steady stream of foam waste to be converted into a valuable commodity with minimal labor.
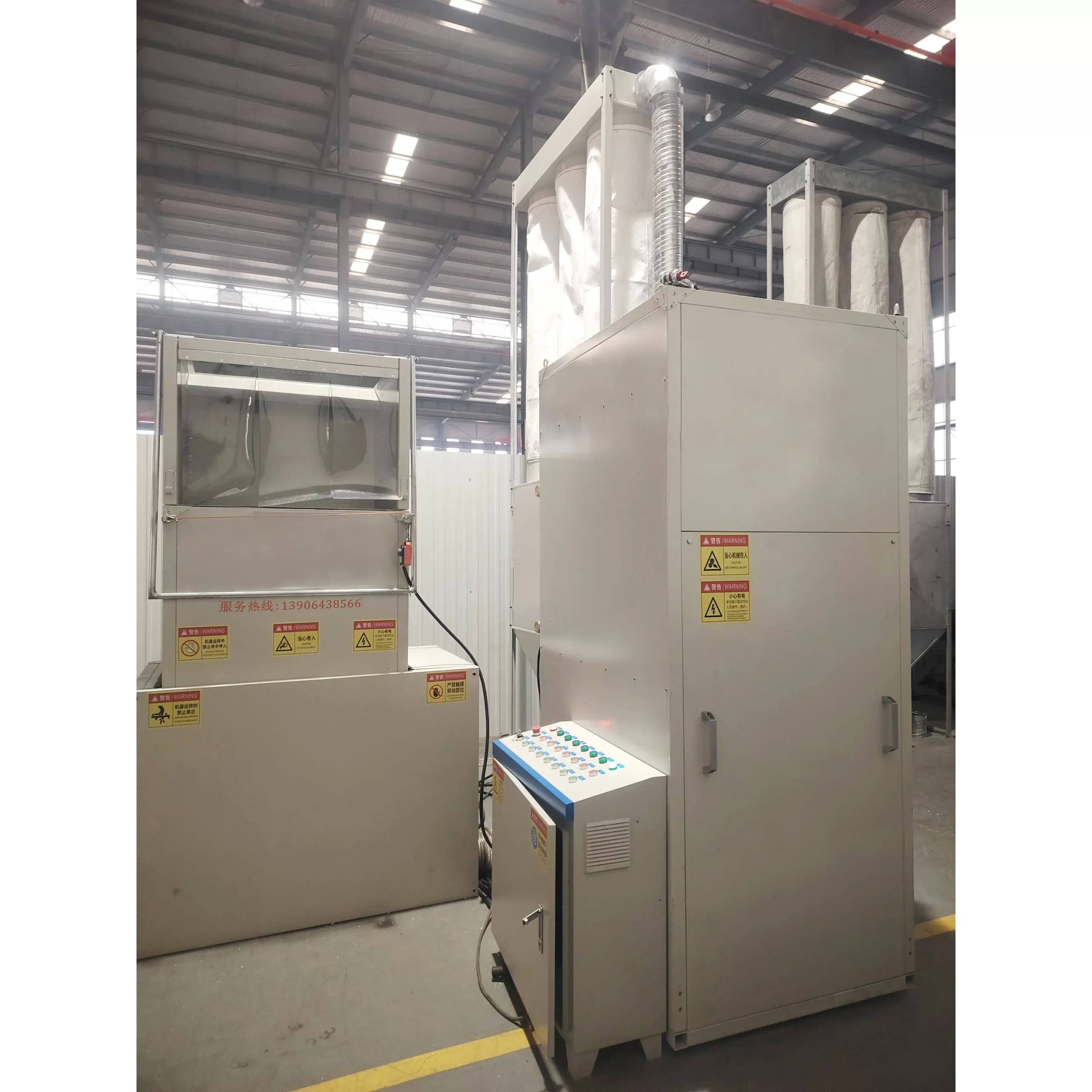
What’s the Difference Between a Foam Compactor and a Densifier?
When exploring foam recycling solutions, you’ll encounter two main types of machines: the foam compactor (also called a cold press) and the foam densifier (a hot melt system). As a manufacturer, I often help clients decide which technology is the best fit. Both recycle foam, but they use different methods and produce slightly different end products.
A Styrofoam compactor uses immense physical pressure to squeeze the air out. Think of it as a super-powered trash compactor specifically designed for foam. The machine uses a screw and a hydraulic chamber to force the EPS into a dense block.
A Styrofoam densifier, on the other hand, uses heat. It shreds the foam and then melts it, causing the material to collapse and release the air. This molten polystyrene is then extruded and cools into a very dense, hard ingot that looks like a piece of solid plastic.
Here’s a table to help you compare:
Feature | Foam Compactor (Cold Press) | Foam Densifier (Hot Melt) |
---|---|---|
Technology | Mechanical screw & hydraulic pressure | Heat and melting |
Compression Ratio | Good (Approx. 50:1) | Excellent (Approx. 90:1) |
Energy Use | Lower | Higher (due to heating element) |
Emissions | None | Requires proper ventilation for fumes |
End Product | Dense, stackable blocks | Extremely dense, solid ingots |
Best For | Most businesses, easy to operate | Operations with high volume, where maximum density is key |
For most businesses, a cold EPS Compactor Machine is the perfect cost-effective solution. It’s simpler, uses less energy, and doesn’t require special ventilation. A foam densifier, or EPS Hot Melt Machine, is better suited for large-scale recyclers who are paid by weight and need to maximize the density of their final product.
Can These Machines Handle Other Foams like XPS and EPE?
This is a fantastic question and one that I get from knowledgeable clients like Mark Thompson, who handle a variety of materials. The answer is yes, absolutely. While we often call them "Styrofoam" recycling machines, their capabilities extend to other common types of plastic foam.
The most common variants you’ll encounter are:
- EPS (Expanded Polystyrene): The beaded white foam we’ve been discussing.
- XPS (Extruded Polystyrene): This is a rigid, often colored (blue or pink) foam insulation board. It has a more uniform, closed-cell structure than EPS.
- EPE (Expanded Polyethylene): A flexible and resilient foam used for packaging delicate items, like electronics. It feels less brittle than polystyrene.
- EPP (Expanded Polypropylene): A highly durable and resilient foam often used in automotive parts and reusable industrial packaging.
Most high-quality foam compactor and densifier models can process all these materials. The key is working with a manufacturer who understands the different properties of each foam. For example, the density and melting point of XPS and EPE differ from EPS. A well-designed machine will allow for adjustments in pressure or temperature to optimally compact each type of material without issue. This versatility makes the investment even more valuable for businesses with diverse waste streams.
What Are the Biggest Advantages of Using a Foam Recycling Machine?
Investing in a foam recycling machine isn’t just about being "green"—it’s a smart business decision with a clear return on investment. As a business owner, you’re focused on the bottom line, and this is where the technology truly shines.
Here are the key benefits you can expect:
- Massive Cost Savings: The biggest and most immediate impact is on your disposal fees. By reducing the volume of your foam waste by a ratio of up to 90:1, you can drastically cut down on the number of waste pickups you need. This translates directly into hundreds or even thousands of dollars saved each month.
- Create a New Revenue Stream: This is the part that turns a cost center into a profit center. The compacted polystyrene blocks or ingots are a valuable commodity. There is a robust market for this material, with recyclers and manufacturers paying good money for it. You can sell your densified foam and generate income from something you used to pay to throw away.
- Optimize Your Floor Space: Loose Styrofoam is a space hog. Bags and bins of foam clutter up valuable warehouse or production space, creating inefficiencies and safety hazards. Compacting it down to a few neat pallets frees up this space for more productive use.
- Improve Your Company’s Environmental Image: In today’s market, sustainability matters. Demonstrating a commitment to recycle and reduce waste can be a powerful marketing tool. It shows your customers, partners, and community that you are a responsible business.
- Increased Efficiency and Safety: A dedicated foam recycling station streamlines your waste management process. It keeps workspaces cleaner, reduces fire hazards associated with loose foam, and creates a more organized and professional environment.
"I’ve worked with many company owners who were initially hesitant about the upfront cost. But within a year, every single one of them told me the machine paid for itself through saved disposal fees and revenue from selling the recycled blocks. It’s a game-changer for operations." – Allen, YouLi Machine Manufacturing
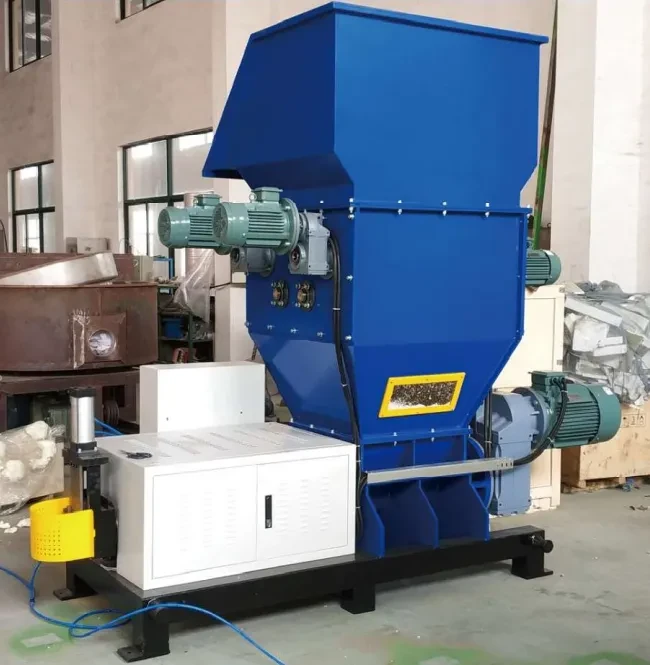
How Do I Choose the Right Styrofoam Recycling Machine for My Business?
Selecting the right recycling machine is crucial. A machine that’s too small will create a bottleneck, while one that’s too large is an unnecessary expense. As someone who guides clients through this process regularly, here is the checklist I recommend you use:
- Assess Your Waste Volume: First, quantify your foam generation. How many bags or bins of EPS, XPS, or EPE do you produce per day or week? This is the single most important factor in determining the required capacity of your machine.
- Identify Your Material Type(s): Are you dealing exclusively with EPS? Or do you also have extruded polystyrene or polyethylene foam? Make sure the machine you choose can effectively handle all your foam types.
- Evaluate Your Space and Utilities: Measure the floor space you have available. Do you have the necessary electrical hookups? For a hot melt densifier, do you have a well-ventilated area?
- Decide Between a Compactor and a Densifier: Based on our comparison earlier, which technology makes more sense for you? For most, the simplicity and lower energy use of a cold foam compactor is ideal. For large-scale recycling centers, a foam densifier might be better.
- Consider the Level of Automation: Do you need a simple, standalone machine where an operator feeds the foam manually? Or would your operation benefit from an integrated system with conveyors and automated feeding? For large-scale production facilities, a fully automatic EPS Recycling Machine with a Crusher and De-duster can offer significant labor savings.
- Vet Your Supplier: This is a point I cannot stress enough. Your relationship with the manufacturer is as important as the machine itself. Ask them about:
- After-Sales Support: What does their installation, training, and technical support look like?
- Spare Parts: How quickly can you get critical spare parts to avoid downtime?
- Experience and Reputation: Have they been in the industry long? Can they provide references?
- Certifications: Does the equipment meet international standards like CE?
What is the Step-by-Step Process to Compact Styrofoam?
Operating a modern Styrofoam compactor is designed to be simple and safe. While specific controls vary by model, the fundamental process remains consistent. Here’s how a typical cycle works:
- Power On: The operator starts the machine via a user-friendly control panel.
- Collection & Feeding: Gather the loose EPS foam waste. An operator takes the Styrofoam pieces and simply drops them into the feed opening, or hopper, at the top of the machine.
- Automatic Crushing: Once the material is in the hopper, the internal shredding blades automatically engage, breaking the foam down into smaller, manageable flakes.
- Compacting: The screw drive motor starts, pulling the shredded foam into the compression chamber. Here, the screw pushes the material forward with immense force, squeezing out the air and forming a dense log.
- Extrusion: As more material is fed in, the compacted log is slowly and continuously pushed out of the extrusion outlet. The extruded block can be cut to a desired length (e.g., one meter) for easy stacking.
- Stacking: The dense, solid blocks are cool to the touch and can be immediately stacked on a pallet, ready for storage or transport.
The process is highly efficient, allowing one operator to process a large volume of foam waste in a short amount of time.
How Much Can a Styrofoam Compactor Really Reduce Foam Volume?
The volume reduction capability of a Styrofoam recycling machine is its most impressive feature. The numbers are truly staggering and represent the core value of the investment.
- A cold press foam compactor can achieve a compression ratio of approximately 50:1. This means it can take 50 cubic meters of loose foam and reduce it down to just 1 cubic meter of dense, stackable blocks.
- A hot melt foam densifier can do even better, reaching a compression ratio of up to 90:1.
To put that into perspective: imagine a standard 40-foot shipping container filled to the brim with loose EPS foam. After processing through a compactor, that same amount of polystyrene material would take up the space of just a single pallet. This is why it suddenly becomes economical to store and transport the material for recycling. You’re no longer paying to ship air.
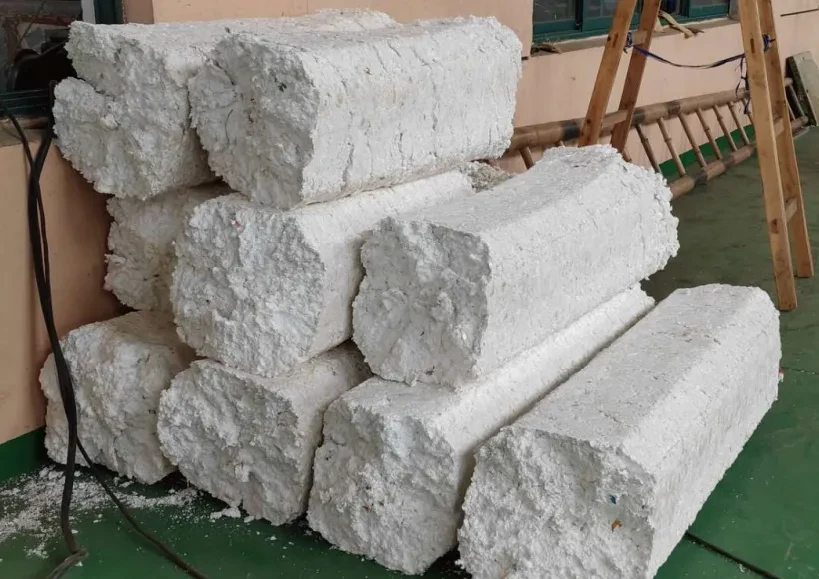
After Compacting, What is the Recycled EPS Material Used For?
This is where the story of foam recycling comes full circle. The dense polystyrene blocks and ingots your machine produces are not waste; they are a valuable raw material. This compacted EPS is known in the recycling industry as "ingots" or "pucks" and is in high demand.
These blocks are sold to recycling companies and manufacturers who shred them, melt them down, and turn them into pellets of recycled polystyrene. These pellets are then used to manufacture a huge variety of new products, including:
- Picture frames and mirror frames
- Architectural moldings (crown molding, baseboards)
- Park benches and outdoor furniture
- Hangers
- Hard-shell protective casings
- New insulation products
- Even some non-food-grade packaging
By investing in a recycling machine, your business becomes a crucial first step in this circular economy. You’re not just saving money; you’re actively supplying the raw material for a new generation of sustainable products.
Why Partnering with a Specialist Manufacturer is Crucial for Success
As someone who has been in the EPS and EPP machinery industry for decades, I’ve seen firsthand how the success of a recycling program hinges on choosing the right partner, not just the right machine. For a business owner like Mark, who values reliability and performance, the manufacturer’s support is paramount.
When you’re making a capital investment, you need more than a seller; you need a partner who understands the technology and is committed to your long-term success. A specialist manufacturer brings several key advantages:
- Deep Expertise: We don’t just sell machines; we design, build, and service them. We understand the nuances of processing different materials like EPS, XPS, and polypropylene, and can configure a machine perfectly for your needs.
- Quality and Reliability: A dedicated manufacturer uses high-quality components and robust engineering to build machines that last. This means less downtime, consistent performance, and a higher return on your investment.
- Comprehensive Support: The relationship shouldn’t end when the machine is delivered. A true partner provides installation support, thorough operator training, and responsive after-sales service. If you have an issue, you need to know you can get a qualified technician or a spare part quickly.
- A Full-Line Perspective: As a Professional EPS Machine Manufacturer, we understand the entire lifecycle of polystyrene—from pre-expansion to molding to recycling. This holistic view allows us to provide better advice and more integrated solutions.
Choosing a low-cost, unsupported machine can lead to the exact pain points many business owners fear: communication breakdowns, performance issues, and costly downtime. Partnering with an established expert ensures you get a reliable product and the support you need to make your foam recycling initiative a resounding success.
Key Takeaways to Remember
- The Problem is Volume, Not Material: Styrofoam (EPS) is 98% air, making it bulky and expensive to dispose of. A recycling machine solves this by removing the air.
- Two Main Technologies: Foam compactors (cold press) are great for most businesses, while foam densifiers (hot melt) offer maximum compaction for large-scale recyclers.
- It’s a Financial Win: These machines save significant money on disposal fees and create a new revenue stream from selling the compacted polystyrene blocks.
- Versatility is Key: High-quality machines can process not only EPS but also other foams like XPS, EPE, and EPP.
- The End Product is Valuable: Compacted foam is a sought-after raw material used to manufacture everything from picture frames to furniture.
- Your Supplier is Your Partner: Choose a manufacturer with deep expertise, a reputation for quality, and a commitment to after-sales support to ensure your long-term success.
Post time: 06-16-2025