Expanded Polystyrene (EPS), often known by the brand name Styrofoam, is a marvel of modern material science. It’s lightweight, an excellent insulator, and provides fantastic protection for goods in transit. However, these same properties make waste EPS a significant challenge. It’s 98% air, making it incredibly bulky and expensive to transport and dispose of. For businesses generating large volumes of EPS foam, this logistical headache can translate into substantial operational costs and a major environmental headache.
But what if you could transform this bulky waste into a valuable, manageable resource? This is where the EPS compactor comes in. This guide, written from my perspective as Allen, a manufacturer with years of experience in the EPS machinery industry, will walk you through everything you need to know. We’ll explore how these machines work, the financial benefits they offer, and how to choose the right partner to help you turn a costly problem into a simple and efficient revenue stream. If you’re looking to reduce waste costs, improve your environmental footprint, and unlock a new source of income, this article is for you.
What Exactly is an EPS Compactor and Why Do You Need One?
An EPS compactor is a specialized piece of equipment designed to tackle the primary problem with EPS foam waste: its volume. Expanded Polystyrene is mostly air, which means a small amount of plastic material takes up a massive amount of space in a dumpster or on a truck. An EPS compactor machine takes this loose, bulky EPS and dramatically reduces its size. It’s a game-changer for any business that deals with significant quantities of polystyrene packaging or manufacturing off-cuts.
Why is this so important? Firstly, there’s the cost. Disposing of voluminous waste is expensive. You pay for dumpster space and frequent collections (or skip
hires). By compacting the EPS, you can fit 40 to 50 times more material into the same space, drastically cutting down on waste management bills. Secondly, there’s the environmental aspect. Mountains of waste Styrofoam heading to the landfill are an unsustainable practice. An EPS compactor is the first and most critical step in the recycle process, turning a product destined for the dump into a sought-after raw material.
For business owners like Mark Thompson, who I often speak with at industry exhibitions, the "why" is simple. It’s about efficiency and profitability. Managing huge bags of lightweight but space-hogging EPS is a logistical nightmare. An EPS foam compactor turns that logistical headache into a simple, manageable process, freeing up valuable floor space and labor hours that could be better spent on core production activities. It’s not just a waste management tool; it’s a business optimization machine.
How Does an EPS Compactor Machine Actually Work?
The process behind an EPS compactor is brilliantly straightforward yet highly effective. While the engineering can be complex, the operational concept is easy to grasp. The goal is to remove the air and densify the plastic. The mil-tek eps1000 polystyrene compactor breaks down and reforms
the material, and our machines operate on a similar, highly efficient principle. The journey from loose foam to a dense block involves a few key stages.
First, the waste EPS is fed into the machine’s hopper. From there, powerful shredding blades or grinders break the large pieces of EPS foam into smaller, more uniform fragments. This pre-crushing step is crucial for ensuring a consistent and efficient compaction process. Once shredded, the material falls into the core of the compactor, which is a chamber containing a large, powerful screw auger.
This is where the magic happens. The screw relentlessly pushes the shredded EPS material forward, applying immense pressure. This force does two things: it physically squeezes the air out of the foam structure and generates friction, which creates heat. This combination of pressure and heat causes the polystyrene to soften and fuse together. The screw then extrudes the densified material through a shaped outlet, forming a solid, continuous log or briquette of compacted EPS. This dense briquette which can be sold
is easy to stack, store, and transport, effectively converting a problematic waste product into a valuable commodity. The entire process is designed to reduce the volume of eps
dramatically.
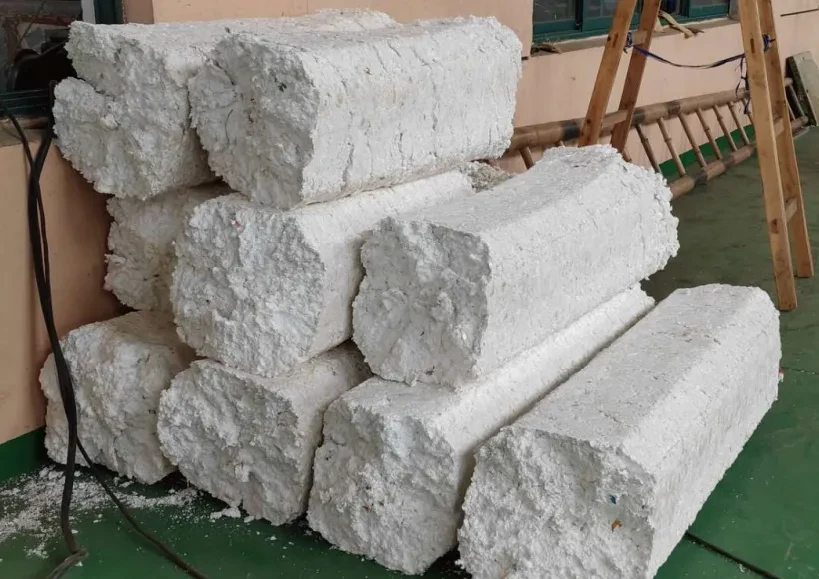
What are the Main Types of Polystyrene Compactors Available?
When you start exploring the market for a polystyrene compactor, you’ll quickly discover there are two primary technologies: cold compactors and hot melt densifiers. Understanding the difference is key to selecting the right machine for your specific needs. As a manufacturer, we produce both types because they serve different operational goals.
- Cold Compactor (Screw Press): This is the most common type of EPS compactor. As described in the previous section, it uses immense physical pressure from a screw to
compress
the foam and extrude it into dense blocks. The "cold" in the name is slightly misleading, as the friction in the process does generate some heat, but it doesn’t actively melt the plastic into a liquid state.- Pros: Lower energy consumption, generally lower initial investment, simpler operation, and produces a high-quality, recyclable briquette.
- Cons: The compaction ratio, while excellent (around 50:1), is typically less than a hot melt machine.
- Hot Melt Densifier: This type of compactor machine also shreds the EPS foam first. However, it then uses a dedicated heating element to melt the polystyrene into a molten state before extruding it. The extruded material cools into an extremely dense, ingot-like form.
- Pros: Achieves the highest possible compaction ratio (up to 90:1), resulting in the densest and heaviest blocks. This can be advantageous for minimizing shipping costs over very long distances.
- Cons: Higher energy consumption due to the heating elements, a higher initial purchase price, and requires more careful ventilation to manage fumes.
For most businesses, a high-quality cold EPS compactor like our EPS Compactor Machine provides the perfect balance of efficiency, cost-effectiveness, and excellent compaction. It transforms loose eps
into a manageable and profitable resource without the higher energy costs of a hot melt system.
Can Investing in an EPS Compactor Truly Generate Revenue?
Absolutely. This is the point that often shifts the conversation from viewing an EPS compactor as an expense to seeing it as an investment with a clear return. The primary way these machines generate revenue is by creating a saleable product from what was previously a waste stream you paid to have hauled away. The compacted EPS
blocks are not trash; they are a sought-after commodity in the plastics recycling market.
Recycling companies and manufacturers actively purchase these dense blocks of compacted polystyrene. Why? Because it’s a clean, pre-processed feedstock. This eps material
can be ground up and re-pelletized to create new products. The compacted styrofoam can be recycled into almost any plastic based product
, including picture frame products and construction moldings
, new packaging materials, and even consumer goods. The material is converted
from waste into a valuable raw material.
Let’s look at a simple hypothetical table.
Metric | Without EPS Compactor | With EPS Compactor |
---|---|---|
Monthly Waste EPS | 5,000 kg | 5,000 kg |
Monthly Disposal Cost | -$1,500 (Landfill/Transport Fees) | $0 |
Compacted EPS Volume | N/A | ~5,000 kg |
Sale Price of Compacted EPS | $0 | +$2,000 (at $0.40/kg) |
Net Monthly Result | -$1,500 | +$2,000 |
Total Monthly Swing | \multicolumn{2}{c | }{+$3,500} |
(Note: Prices are illustrative and fluctuate based on market conditions.)
This table clearly shows the shift. You eliminate a significant monthly cost and create a new revenue stream. For a business owner, this is a powerful proposition. An EPS foam compactor doesn’t just save money; it makes money. It turns a financial drain into a simple and efficient revenue stream
.
How Does Compacting EPS Significantly Reduce Your Operational Costs?
Beyond direct revenue generation, an EPS compactor delivers substantial operational cost savings that directly impact your bottom line. These savings are immediate, measurable, and compound over time. The primary benefit comes from the drastic volume reduction. Think about your current EPS disposal process: employees spend time gathering bulky foam, placing it in large bags or bins, which then take up a huge amount of expensive floor space before being moved to an equally large dumpster.
Here’s how a polystyrene compactor
slashes those costs:
- Reduced Waste Collection Fees: The most direct saving. If you currently pay for two dumpster pickups per week for your EPS foam waste, compacting the material could reduce that to one pickup a month, or even less. You are no longer paying to transport air. This can lead to
substantial savings
on yourwaste costs
. - Optimized Labor and Workflow: Your staff’s time is valuable. An EPS compactor streamlines the waste handling process. Instead of managing unwieldy bags of foam, an employee can simply feed the EPS into the compactor as it’s generated. This improves your internal workflow and frees up your team to focus on value-adding tasks.
- Reclaimed Floor Space: Warehousing and production space is a premium asset. Piles of EPS waste consume a surprising amount of it. The dense, stackable blocks produced by a compactor take up a fraction of the space, allowing you to use that reclaimed area for storage, production, or other profitable activities.
- Lower Transportation Costs: If you transport waste between facilities or directly to a recycler, the logic is simple. A truck that could only hold 1,000 lbs of loose EPS can now hold 40,000 lbs of compacted EPS. This makes the material much
easier to transport
and significantly reduces per-pound shipping costs, making your recycled material more profitable when yousold for recycling
.
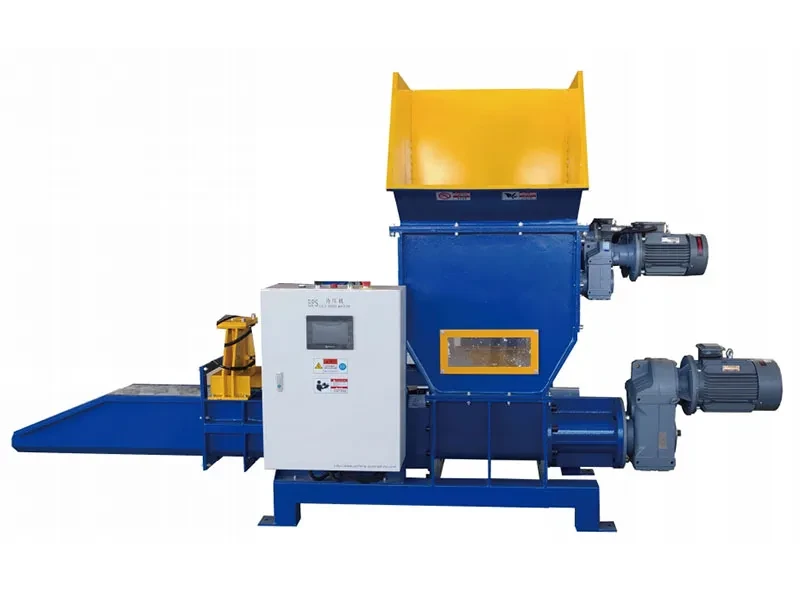
What Should You Look for When Choosing the Right EPS Foam Compactor?
Choosing the right EPS foam compactor is a critical decision. It’s a long-term investment in your operational efficiency. As a manufacturer, I’ve seen firsthand what separates a reliable, high-performing compactor from one that causes constant headaches. When I talk to potential customers like Mark, I advise them to look beyond just the price tag and evaluate the machine on several key factors.
Here is a checklist of what to consider:
- Throughput and Capacity: How much EPS waste do you generate per hour or per day? Be realistic. Choose a machine that can comfortably handle your peak volumes without being constantly overworked. An undersized compactor will become a bottleneck.
- Build Quality and Durability: Look closely at the construction. Is the frame made from heavy-gauge steel? Are the components, especially the screw and chamber, made from hardened, wear-resistant metals? A well-built EPS machine will provide years of reliable service.
- Motor and Gearbox Power: The motor is the heart of the compactor. A powerful, high-quality motor and a robust gearbox are essential for handling dense material and ensuring consistent compaction without stalling or overheating.
- Safety Features: This is non-negotiable. The machine should have emergency stop buttons, safety interlocks on the hopper, and clear warnings. If you’re in Europe or exporting there, CE certification is a must, as it indicates compliance with high safety standards.
- Ease of Use and Automation: The machine should be simple to operate. Look for a user-friendly control panel and features like automatic cut-off sensors. The goal is to make the recycle process efficient, not to create a complex new task for your staff. The
mil-tek eps1000 allows
for simple operation, and any quality machine should aim for that level of user-friendliness. - Supplier Reputation and Support: Who are you buying from? Do they have a proven track record? Can they provide case studies or references? A reliable supplier will stand behind their product with excellent after-sales service.
Are There Different Compactors for Different Types of EPS Waste?
This is a great question we often get. While the fundamental principle of the EPS compactor remains the same, the source and form of the EPS can influence the ideal machine configuration. The good news is that a well-designed polystyrene compactor is incredibly versatile and can handle most forms of clean EPS foam waste.
For instance, many businesses use eps6 for packaging
. This includes electronics manufacturers
, furniture companies, and appliance distributors who use protective and insulating polystyrene packaging
. This type of EPS is typically clean but can come in large, awkward molded shapes. A compactor with a powerful pre-shredder is essential here to break down these bulky items before compaction. Similarly, businesses in food processing
that use EPS fish boxes need a machine that can handle this specific shape.
In our own manufacturing lines, we see a different kind of waste. When we run a Best Sale EPS Cutting Line, there are off-cuts and dust generated. This material is also perfect for a compactor. The mil-tek eps1000 shreds
and compacts material effectively, and our EPS compactor systems are designed with the same goal: to handle whatever form of EPS you have. The key is to ensure the compactor’s infeed hopper and shredder are robust enough for your specific type of waste styrofoam
. The eps1000 polystyrene compactor compacts
a wide variety, and a quality machine should do the same.
How Does a Compactor Fit into a Complete EPS Recycling Workflow?
An EPS compactor is a crucial piece of the puzzle, but it’s important to see it as part of a larger, circular process. It’s the bridge between generating waste and creating a recycled product. Understanding this complete workflow helps you appreciate the machine’s full value.
Here is the typical lifecycle of EPS once a compactor is introduced:
- Waste Generation: Your business operations—whether it’s unpacking goods or manufacturing with EPS—create
loose eps
scrap. - Collection & Feeding: Instead of bagging it for the landfill, this EPS foam is collected and fed directly into the EPS foam compactor.
- Compaction: The compactor does its job, shredding the foam and compressing it into dense, stackable blocks or briquettes. The
eps1000 compacts
the material,reduce the size
, and makes it manageable. - Storage & Accumulation: These dense blocks are neatly stacked on a pallet. You can now store a large weight of EPS in a very small footprint, waiting until you have a full truckload.
- Sale and Transportation: Once you have a sufficient quantity, the compacted EPS block is sold to a specialized recycler. Because it is so dense, it can be transported very cost-effectively.
- Recycling Process: The recycler takes your blocks and grinds them into small beads. These beads are then melted, filtered, and extruded into new plastic pellets (recycled polystyrene or rPS).
- New Product Manufacturing: These rPS pellets are the raw material for new products. They can be
recycled into plastic components such as electronics
, picture frames, park benches, and even some types of insulation. Thepolystyrene compactor compacts and converts
a single-use item into a resource for many new applications.
This entire process starts with one key machine: the EPS compactor. Without it, the volume of eps waste
makes the logistics of recycling prohibitively expensive.
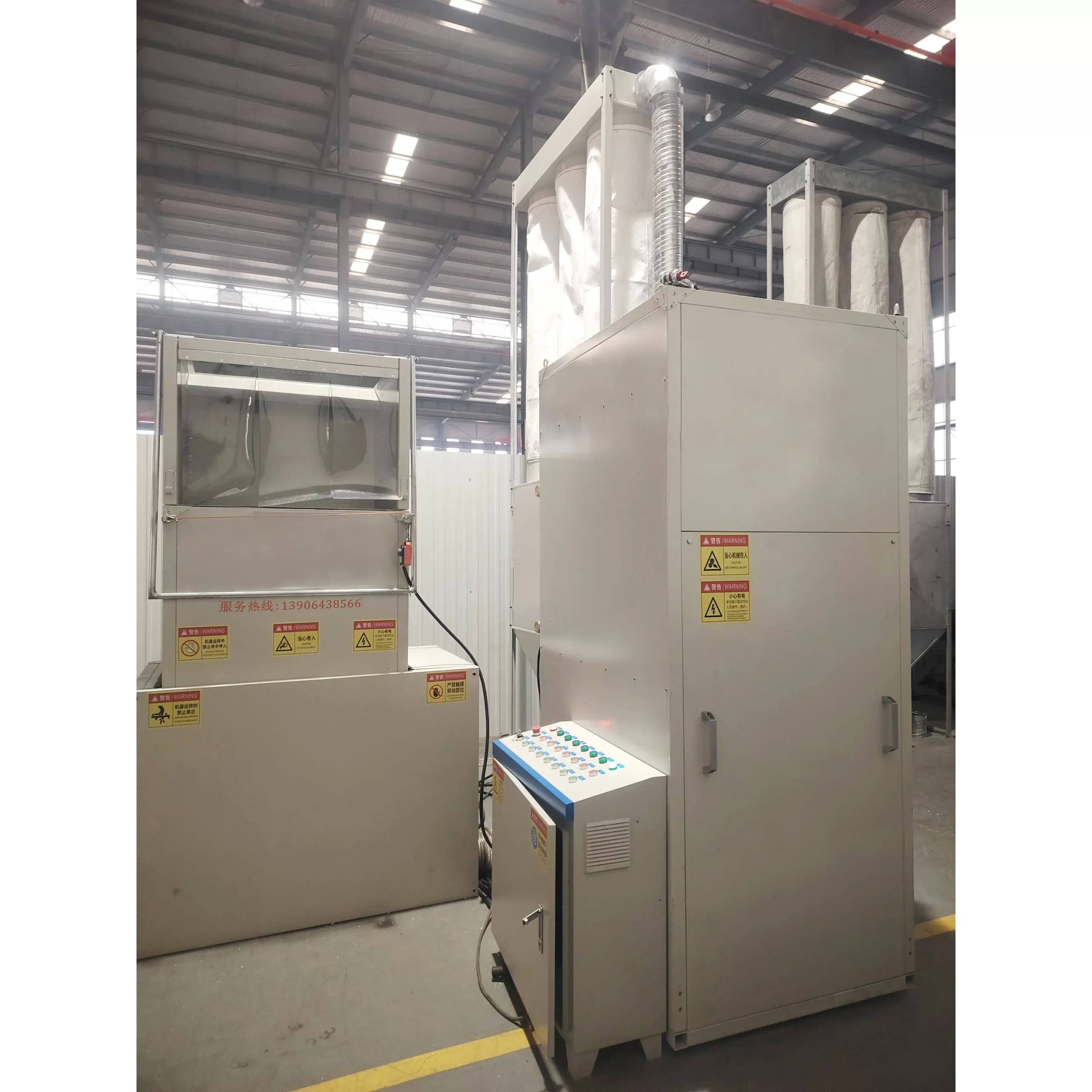
What are the Biggest Mistakes to Avoid When Buying an EPS Compactor from Overseas?
As a manufacturer in China who exports globally, I understand the concerns of buyers like Mark in the USA. Purchasing heavy machinery from an international supplier can feel risky. The potential for cost savings is significant, but so are the potential pitfalls if you don’t choose your partner wisely. Based on my experience, here are the biggest mistakes to avoid.
- Prioritizing Price Over Everything: It’s tempting to go for the cheapest option, but this often leads to disappointment. An ultra-low price can be a red flag for inferior materials, underpowered motors, or a lack of safety features. The total cost of ownership—including maintenance, downtime, and lifespan—is far more important than the initial purchase price. A slightly more expensive but reliable compactor will be cheaper in the long run.
- Ignoring Communication: Can you communicate clearly with the sales and technical teams? Inefficient communication is a major pain point. If they can’t answer your questions clearly and promptly before the sale, it’s unlikely their after-sales support will be any better. Ensure they understand your technical requirements and can provide documentation in clear English.
- Failing to Verify the Supplier: Don’t just rely on a website. Ask for a virtual factory tour. Request references from customers in your country or region (USA, North America, Europe). A legitimate, proud manufacturer will be happy to showcase their facilities and connect you with satisfied clients. This simple step can save you from a lot of trouble.
- Overlooking Spare Parts and Support: A machine is only as good as its weakest part. Before you buy, ask about the availability and cost of common wear parts like blades and screw components. What is their procedure for providing technical support? Do they have engineers who can help diagnose problems via video call? A supplier who can’t give you a clear answer on this is a risk. We ensure a stock of critical parts for all our machines, including our full range of EPS and EPP machinery.
Why is Proper Training and After-Sales Support Crucial for Your Compactor?
The relationship with your supplier shouldn’t end once the EPS compactor is delivered. The final, and perhaps most critical, element for long-term success is the quality of training and ongoing support. A powerful machine is useless if your team doesn’t know how to operate it safely and efficiently, or if a minor issue leads to prolonged downtime because you can’t get help.
Proper training ensures your operators understand the machine’s functions, daily maintenance checks (like cleaning the screw), and safety procedures. While some articles might mention a mil-tek technician
, the best support comes directly from the people who built your machine. We provide comprehensive manuals and video support to ensure our clients can get up and running smoothly. This initial training prevents common operator errors and maximizes the life of the compactor.
After-sales support is your insurance policy against downtime. What happens if a sensor fails or you encounter an unusual issue? A responsive support team that can help you troubleshoot the problem quickly is invaluable. This is a core part of our business philosophy. Using a mil-tek eps1000 polystyrene
machine is one option, but a partnership with a manufacturer who provides dedicated support for their EPS compactor machine ensures you have a resource for the entire life of the equipment. Investing in a machine from a supplier who invests in you is the key to a successful, profitable recycling operation. Remember, the goal is to dispose
of your waste problem, not create a maintenance one. The right partner ensures your mil-tek eps1000 polystyrene compactor breaks down and reforms eps6 into a briquette
reliably for years to come.
Key Takeaways
Investing in an EPS compactor is one of the smartest decisions a business generating polystyrene waste can make. It’s a strategic move that addresses environmental responsibilities while directly improving your financial performance.
- Turn Waste into Wealth: An EPS compactor transforms costly EPS foam waste into a saleable commodity, creating a new revenue stream.
- Drastically Cut Costs: You will significantly reduce or eliminate landfill and waste transport fees, saving your company thousands of dollars annually.
- Improve Operational Efficiency: Reclaim valuable floor space, streamline your workflow, and free up your staff from managing bulky waste.
- Boost Your Green Credentials: Taking proactive steps to recycle EPS demonstrates a commitment to sustainability, which is increasingly important to customers and partners.
- Choose Your Partner Wisely: The success of your investment hinges on choosing a high-quality, durable machine from a reliable manufacturer who provides excellent training and long-term support. The
mil-tek logo are registered trademarks of mil-tek
, but the principle of quality and support applies to any brand you choose.
Post time: 06-20-2025